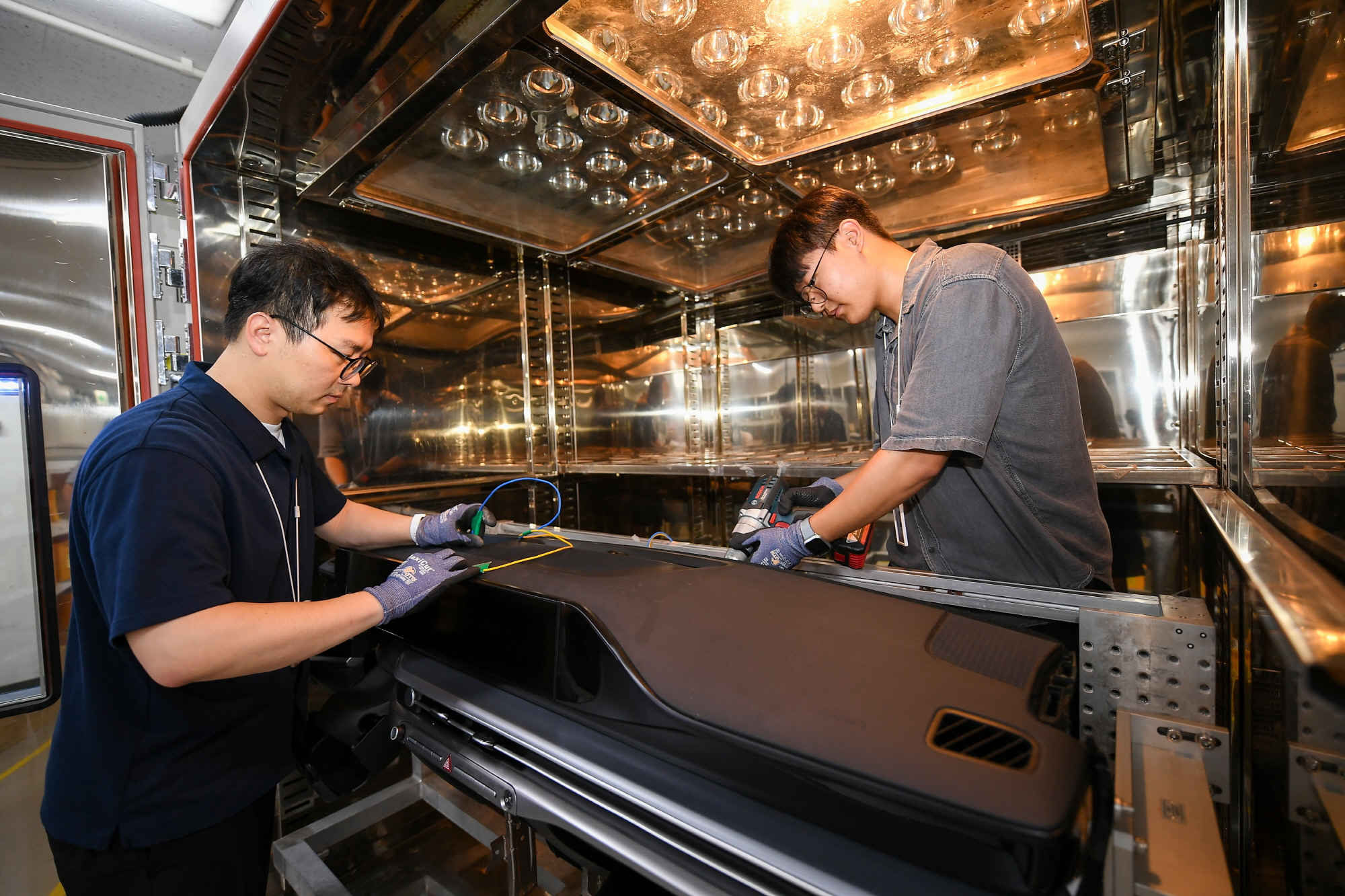
Hyundai Mobis is accelerating the development of new materials for future mobility and has achieved various research and development milestones. This proactive approach enables them to respond ahead of expected global environmental regulations ramping up around 2030. They are enhancing competitiveness in future mobility through high-performance, efficient material technologies, and have been evaluated for their flexibility in addressing trade disputes and international conditions in the raw materials sector.
On the 27th, Hyundai Mobis announced its three major material development strategies to strengthen its core competencies in materials, which are vital for key automotive components: sustainable materials that can respond to global environmental regulations, innovative materials leading mobility, and digital materials realized through virtual verification methods.
Kim Mi-ro, director of R&D at Hyundai Mobis, stated, “The transition to digital technology is changing the paradigm along with environmental-friendly material development for ESG compliance, and we will enhance mobility competitiveness by diversifying materials and reducing external dependencies.”
Hyundai Mobis’ material development strategy aligns with the increasing emphasis on securing independent competitiveness in materials, parts, and equipment, which has been highlighted in recent years. Despite the pandemic, Hyundai Mobis has successfully built a stable supply chain and is achieving independent results in the field of new materials research and development.
The company aims to respond to global environmental regulations by developing sustainable materials, which involve utilizing recycled materials or bio-based materials.
First, recycled materials are mainly used in plastic components. Parts that can be recycled from household waste or scrapped vehicles are collected, processed into smaller pieces, and then mixed with additives to create regenerated materials.
Recently, Hyundai Mobis succeeded in developing a lower arm protective cover that prevents scratches on the bottom of the vehicle using this method. This product contains 50% recycled plastic but maintains the same physical properties as existing products. The European Union is currently pushing legislation requiring that 25% of the plastic used in new cars be made from recycled materials starting in 2030. Hyundai Mobis has surpassed this standard by successfully developing new materials six years ahead of schedule.
Moreover, Hyundai Mobis is developing about 30 types of new materials applicable to components such as cockpit modules, lamps, and airbags that make extensive use of plastic. In the eco-friendly bio sector, they are also focusing on utilizing wood to reduce carbon dioxide emissions while enhancing the durability of eco-friendly materials against weather effects (such as discoloration or decomposition by heat or ultraviolet rays).
Hyundai Mobis is accelerating the conversion of its portfolio toward high value-added products centered on electrification and electronic components, pushing to develop new materials that improve performance while using less scarce metals like nickel.
Recently, Hyundai Mobis developed a new material for inductors, which are key components for power conversion in electric vehicles, that reduces the use of expensive nickel metal. Inductors are made using nickel-mixed metal powders, and Hyundai Mobis has succeeded in reducing the nickel content from 50% to 30%. With nickel prices having surged about six-fold in the last ten years, this new material minimizes raw material price volatility while securing electromagnetic properties.
Furthermore, Hyundai Mobis has reportedly embarked on evaluations for a world-first ‘nickel-free’ new material that does not contain nickel at all. They are also focusing on developing new materials that enhance competitiveness across all areas of electrification and electronic components, including high-speed charging battery cooling technologies, electromagnetic shielding materials, and surface coating technologies for autonomous driving sensors.
Additionally, Hyundai Mobis is dedicated to digital material technologies, integrating IT technologies into traditional material fields. They are simulating and predicting various material properties used in automotive parts virtually to improve consistency.
Innovatively, they are also exploring new materials using artificial intelligence. They automatically assess material properties by quantifying data collected over time. A revolutionary change in material development is expected based on an information platform in the material technology field.
Hyundai Mobis has notably more than 100 materials engineering R&D personnel, which is unusual for an automotive parts company, to strengthen its new material development capabilities. As the scope of R&D expands into digital materials, hiring professionals from diverse fields is also actively being pursued.
As a result of these research and development achievements, Hyundai Mobis was selected as an excellent research laboratory for safety management by the Ministry of Science and ICT, which is unusual for domestic company research facilities. They built a standard model necessary for laboratory operation and were certified as a facility with outstanding R&D management capabilities.
Lee Sang-jin daedusj@autodiary.kr