On the morning of the 3rd, just as dark clouds gathered, I visited the Electric Vehicle Diagnostic Center located within Jeju National University.
The Korea Institute of Production Technology was established in 1989 under the Ministry of Trade (now the Ministry of Industry and Trade). It provides policies and technical support to foster small and medium-sized enterprises. It operates 50 centers nationwide, and the electric vehicle diagnostic center was built within Jeju National University in 2019, covering an area of 4,577m².
The Electric Vehicle Diagnostic Center was established to promote the adoption of electric vehicles and support Jeju’s strong push for a ‘carbon zero’ policy. Hong Young-seon, the center director, stated, “It was built to stabilize the maintenance and repair quality of electric vehicles.”
Upon arrival at the research wing, the Kona EV was on the lift, battery removed, ready for inspection. The battery was separately prepared for testing. The aim is to age the individual cells of the detached battery and then reattach it to evaluate the performance of the aged electric vehicle battery.
A prominent experiment is the lifespan deterioration test of cylindrical cells under varying temperature and humidity conditions. Director Hong emphasized, “Even if just one battery cell is aged, the overall performance of the battery is reduced by half,” highlighting the importance of battery management.
Next to this is a large monitor displaying a map of Jeju City. On the monitor, arrows indicate a consistent direction. Director Hong explained, “This is data collection from electric taxis that are currently in operation.” GPS is attached to these electric taxis, which generally exhibit a significantly greater mileage compared to regular electric passenger cars, allowing their data to be gathered.
The Electric Vehicle Diagnostic Technology Center collects such data from electric taxis to optimize the data foundation and predict failures in the electronic components of electric vehicles. Furthermore, this collected information serves to inform drivers, preventing significant faults from occurring. Additionally, this data provides mechanics with insights into how to repair the vehicles.
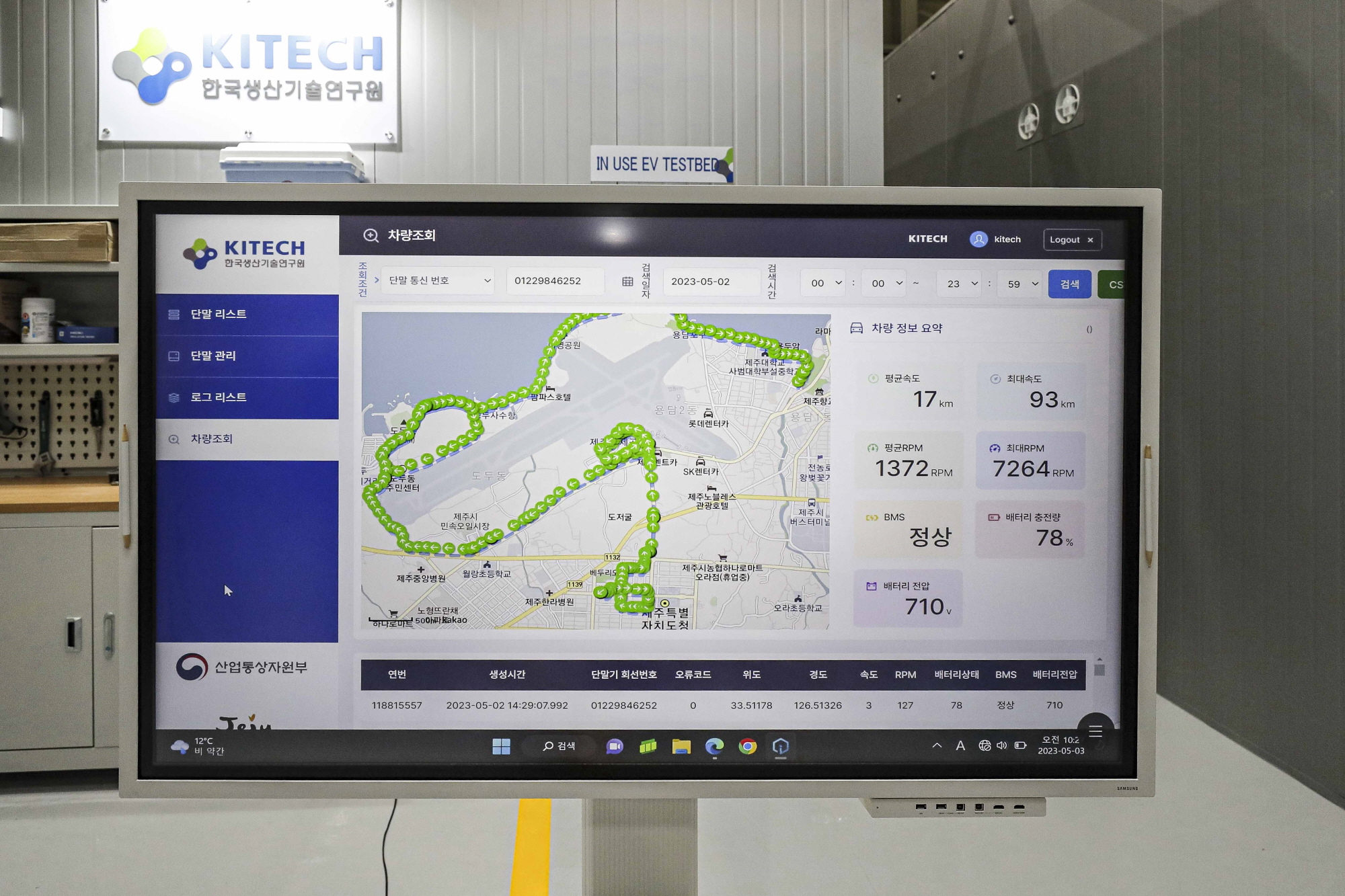
We then visited the Electric Vehicle Drive Simulation Equipment Room. An Ioniq 5 was mounted on a chassis dynamometer, allowing for output and power testing. This is akin to a person getting onto a treadmill. The vehicle is placed on the dynamometer to conduct tests for energy efficiency and evaluate performance. Additionally, fault types, vehicle faults, and parts evaluations can be conducted.
The Electric Vehicle Drive Simulation Equipment Room is equipped with various devices, including vehicle communication and automation control systems, electric vehicle output analysis devices, and real vehicle cooling systems such as cooling fans, enabling real-time monitoring of the vehicle’s condition.
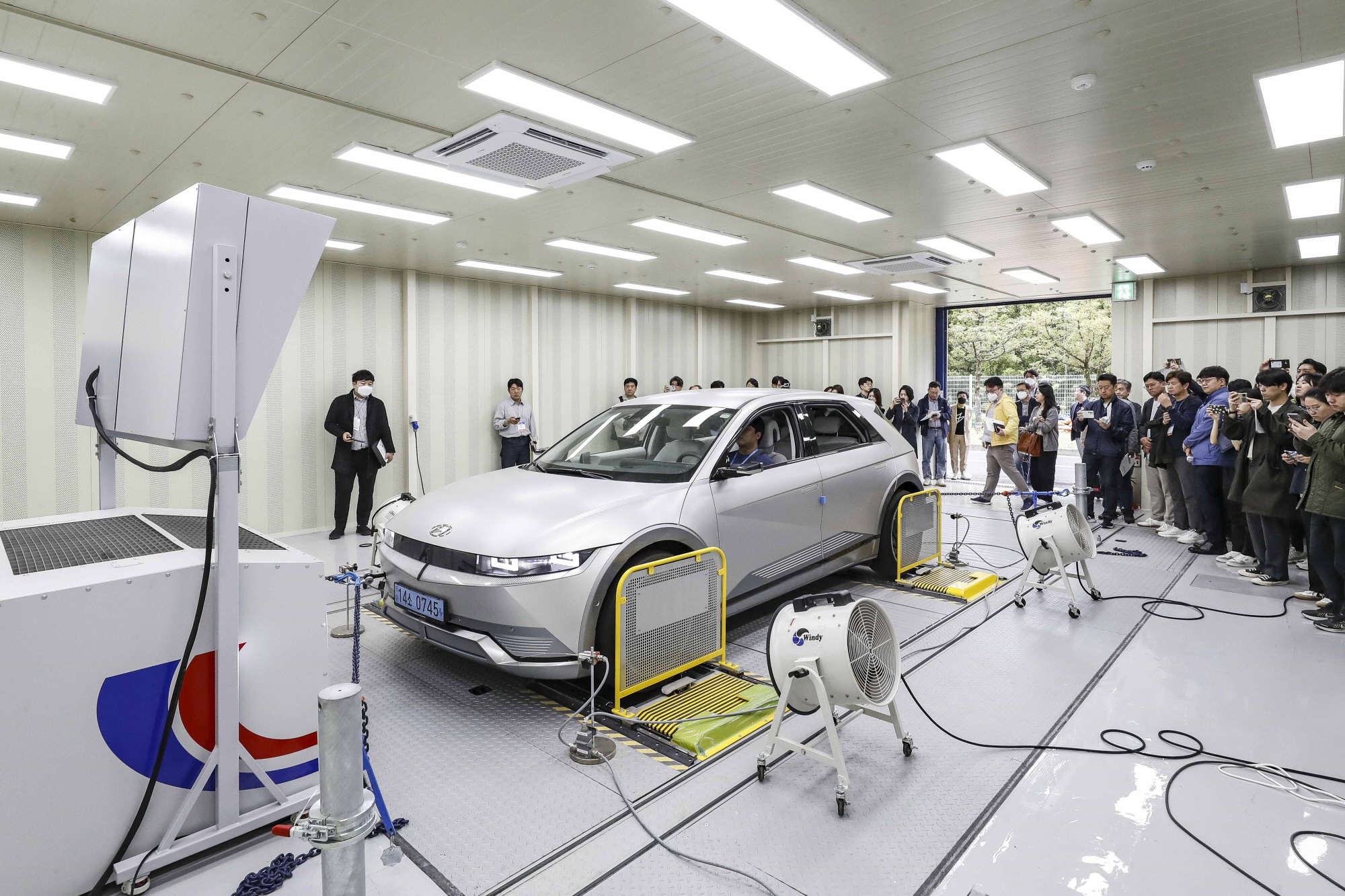
The demonstration of the energy efficiency testing drive followed. A researcher seated in the driver’s seat, alongside a sign from the lab outside, eagerly pressed the accelerator as the engine started.
With the increasing sound of the motor, the Ioniq 5 raced vigorously atop the chassis dynamometer. Simultaneously, the cooling fans placed facing each wheel also spun vigorously. In this manner, various electric vehicle models, including those with aged battery cells, are mounted on the chassis dynamometer for inspection.
Maintenance and repair issues are crucial for electric vehicles. According to the diagnostic center, 39% of quality issues in electric vehicles stem from motors, while 27% are attributed to batteries. The center believes that quality stabilization has not yet reached the level of internal combustion engines.
Jeju = Lee Sang-jin daedusj@autodiary.kr