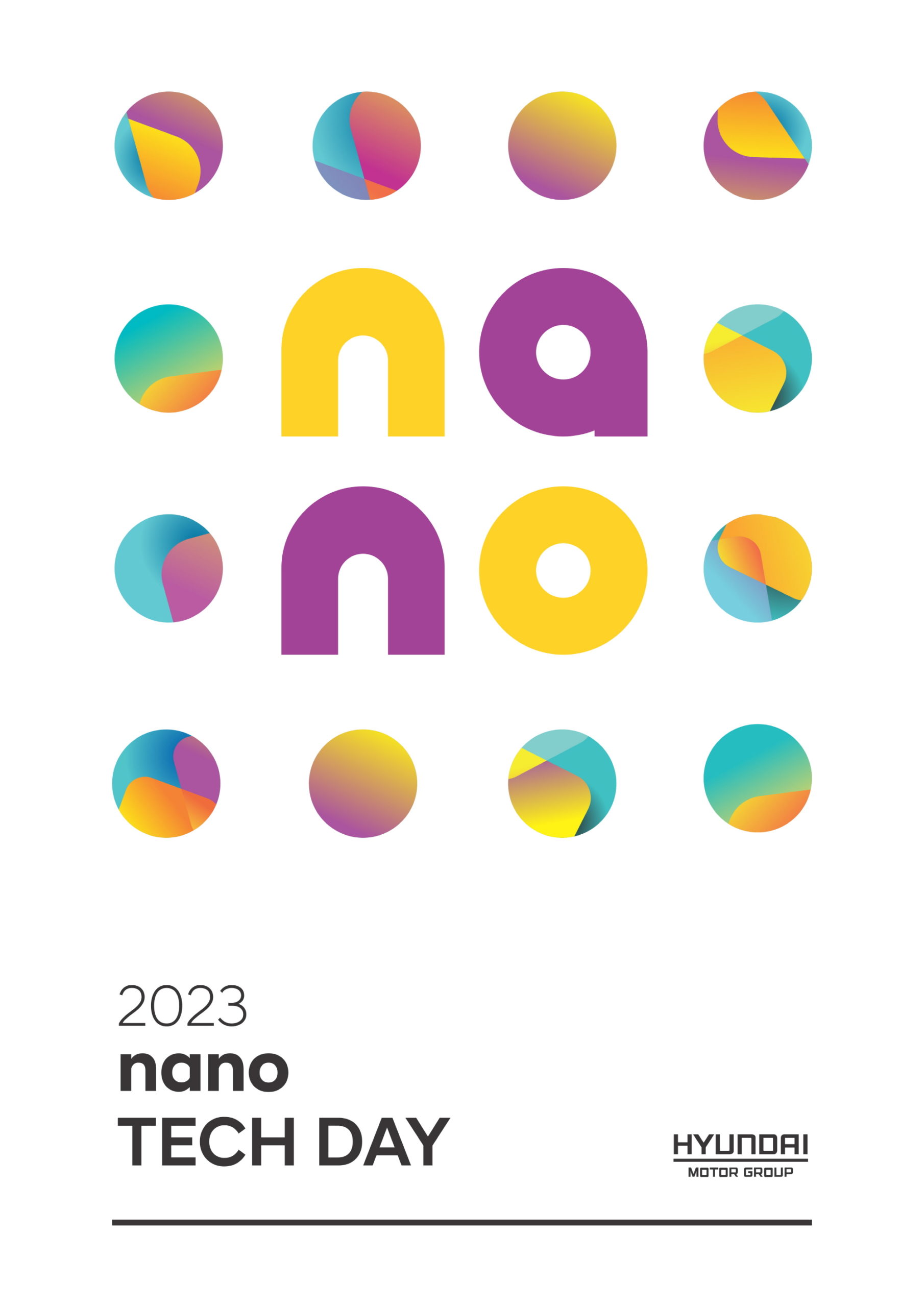
On the 20th of this month, Hyundai and Kia hosted the ‘Nano Tech Day 2023’ at the Community House Masil in Myeongdong, Seoul, unveiling a range of innovative nanotechnologies that will serve as the foundation for future mobility.
One nanometer is one billionth of a meter, equivalent to one hundred thousandth the diameter of a human hair. Nanotechnology involves synthesizing and arranging materials at this tiny scale to create substances with new properties.
This event was themed around the ‘Nano Effect,’ inspired by the ‘Butterfly Effect,’ which posits that slight changes in initial conditions can lead to vastly different outcomes. It highlights the importance of materials technology in the quickly evolving mobility industry and how it can create differential competitiveness in finished products.
Hyundai and Kia introduced a total of six nanomaterial technologies with different purposes and functionalities, facilitating hands-on experiences in a separate exhibition space.
Among them were the ‘Self-Healing Polymer Coating,’ which autonomously heals damaged areas, the ‘Oil Capsule Polymer Coating’ that significantly reduces part wear using nanocapsules, the ‘Transparent Solar Cell’ applicable to all windows requiring transparency in cars and buildings, the ‘Tandem Solar Cell’ boasting world-class efficiency for mobility applications, the ‘Pressure-Sensitive Material’ that detects users’ biosignals solely through pressure, and the ‘Transparent Radiative Cooling Film’ that dramatically minimizes temperature increases inside vehicles.
Hyundai and Kia have been conducting materials research since the 1970s, and they established dedicated teams in the late 1990s focused on advanced materials, embarking on large-scale investments and diverse research projects.
The motivation behind Hyundai and Kia’s commitment to developing advanced materials technology, including nanotechnology, is rooted in the belief that materials are the starting point for all mobility innovations. Future mobility innovations such as electrification, Software-Defined Vehicles (SDVs), and autonomous driving can only be fully realized with materials technology as a fundamental foundation.
By understanding and improving material characteristics at the material stage, potential problems can be anticipated and prevented when they are made into components or finished products. Moreover, the overall quality can be enhanced when the optimal materials are combined with various technologies.
Hyundai and Kia particularly believe that the solutions to lead the rapid changes in the mobility industry, such as the transition to electrification and carbon neutrality, can be found in materials technology. Thus, they are intensifying their research in new materials development and eco-friendly technologies.
In a welcoming address, Lee Jong-soo, the Vice President of Hyundai and Kia’s Advanced Technology Center, stated, “At the core of technological innovation lies materials innovation, which is both fundamental and a key link to industrial convergence. We will continue to proactively develop excellent advanced materials technology to be actively applied in future mobility as industry changes arise.”
While the competition is fierce in the fields of autonomous driving and electrification, the technological advancements are surpassing previous standards. However, even minor scratches or wear on critical components can lead to catastrophic failures. For instance, small scratches on sensors like cameras and LiDAR can adversely affect accurate assessments of external environments. Additionally, electric vehicles with high-speed motors require durability and wear resistance for power components.
Hyundai and Kia presented two polymer coating technologies using nanomaterials to address these issues, mimicking living organisms that heal themselves and creating lubricating films as capsules burst at friction points.
With nanotechnology that helps maintain the vehicle’s condition as if it were brand new, it is expected to enter the market quickly due to its contributions to customer convenience, safety, and the emotional appeal it offers.

The Self-Healing Polymer Coating is a technology that heals damaged areas independently when the vehicle’s exterior or components are harmed.
The self-healing technology developed by Hyundai and Kia can recover in just over two hours at room temperature, even without a separate heat source or curing agent, offering a semi-permanent healing capability.
This technology utilizes the property of self-healing materials, wherein the split polymers attempt to return to their original state through chemical reactions when a scratch occurs on the coated components.
Self-healing technology has been commercialized in the past. However, existing technologies relied on encapsulated agents or vascular-type mechanisms that only worked once, leading to difficulties in repeated healing after initial use. Furthermore, some technologies attempted by other manufacturers required separate heating systems, limiting application to restricted areas like front grilles.
Hyundai and Kia expect to provide differentiated customer value by applying self-healing technology to various areas, overcoming such limitations and enhancing competitiveness.
Initially, they are considering applying this technology to the surfaces of critical components such as camera lenses and LiDAR sensors, as they believe this will have the most significant effect on customer safety. Plans are in place to expand the range of applications to vehicle paint surfaces and external grilles in the future.
Additionally, ongoing research aims to maintain self-healing performance even in harsh environments while adding functions such as water repellency and insulation.

The Oil Capsule Polymer Coating is a spin-off technology developed from researching nanocapsules for self-healing. This technology enhances components by providing low friction and wear resistance, thereby increasing product value. When the polymer coating containing oil capsules is applied to the component surface, the oil capsule bursts during friction, releasing lubricating oil to form a lubrication film.
Currently, vehicles utilize lubricants that are tailored to the movement characteristics of components. Semi-solid lubricants like grease are applied to parts where liquid lubrication is unfeasible, but these are challenging to manage concerning refilling, exchanging, and cleaning, and they provide less cooling performance compared to liquid lubricants, making them unsuitable for high-speed rotating components. Solid lubricants are used in parts that must withstand high temperatures and pressures, but they often present a significant cost burden.
The oil capsule technology developed by Hyundai and Kia combines the advantages of both liquid and solid lubricants. By including liquid lubricating elements within the nano capsules, it achieves high lubrication effectiveness at lower costs and allows for application across a wide range similarly to solid lubricants.
The Oil Capsule Coating offers durable lubrication effects over extended periods. Tests conducted by Hyundai and Kia have shown that the oil capsule coating applied to components maintains its lubricating functionalities throughout the component’s lifespan without wearing away.
This technology is expected to improve durability and efficiency when applied to core power transmission components of vehicles that experience significant heat and friction. Primarily, it aims to reduce rotational losses in electric vehicle motors and gearboxes, thus enhancing overall energy efficiency and significantly increasing parts longevity.
Hyundai and Kia are developing products targeting mass production by applying this technology to drive shafts that transmit engine power to the wheels. They are also considering incorporating fragrant nano capsules into interior materials so that diverse scents can be experienced with each touch.

In the electric vehicle market, expanding driving range and reducing charging time are considered key competitive advantages. Current electric vehicle energy systems heavily rely on batteries, making significant energy improvements challenging under the current circumstances. Additionally, the increase in electronic devices is raising power consumption, necessitating advanced technology development to enhance energy efficiency.
Hyundai and Kia are researching highly efficient energy generation technology based on solar cells to achieve true eco-friendly mobility. The nano-based solar cells unveiled during this event can be used in electrified vehicles as well as buildings, identifying them as technologies with tremendous future growth potential.
Until now, most solar cells have been produced using silicon materials, making them unsuitable for applications requiring transparency, like windows in buildings or glasses on vehicles.
Hyundai and Kia showcased their ‘Transparent Solar Cell’ technology that uses perovskite materials with excellent electrical and optical properties.
Perovskite is known for its high photovoltaic efficiency, which can result in energy generation efficiency over 30% higher than that of silicon solar cells when made into solar panels. Consequently, many major universities and energy companies globally are in competition to develop solar cell technologies using this material.
Hyundai and Kia are continuing research to maximize the transparency of perovskite materials. By adjusting the thickness of the photo-absorbing layer, they achieved a dual result of optimizing solar power generation while maintaining physical transparency.
The significance lies in the development of large-area (over 200 cm²) transparent solar cells, moving beyond conventional small-area (1 cm²) research. They have produced transparent solar cells that demonstrate performance equivalent to 1.5 watts in module form, marking the world’s first achievement.
The potential applications for transparent solar cells are vast. While opaque silicon solar cells have only been applicable on the roofs of electrified vehicles, transparent solar cells can be applied to all glass surfaces of vehicles to maximize electricity generation efficiency for electric cars.
Furthermore, by replacing building windows, this technology could reduce energy consumption while seamlessly blending into architectural designs. To this end, Hyundai and Kia are collaborating with companies like Hyundai Engineering & Construction on various research initiatives.
Despite the advantage of being able to obtain sustainable energy, solar cells face the challenges of low efficiency. As conventional silicon solar cells are believed to have reached their efficiency limits, there is a global push to develop next-generation solar cells with innovative approaches.
Hyundai and Kia are focusing on ‘Tandem Solar Cells’ created by stacking the next-generation solar material perovskite onto silicon solar cells. This technology allows two solar cells to absorb different spectral ranges of sunlight complementarily, achieving energy efficiencies exceeding 35%.
In collaboration with UNIST (Ulsan National Institute of Science and Technology), Hyundai and Kia launched a joint research laboratory in 2022 to develop high-efficiency tandem solar cells. Their in-house evaluations have recorded energy efficiency levels exceeding 30%, ranking them among the best globally.
Hyundai and Kia predict that merely applying tandem solar cells to areas directly exposed to sunlight, such as hoods, roofs, and doors of eco-friendly vehicles, will yield sufficient power for daily commuting. Currently, they aim to secure an additional driving range of over 20 km based solely on average daily solar energy generation (based on domestic average sunshine of 4 hours).
If tandem solar cells are applied to large electric commercial vehicles with extensive glass areas, more significant power generation effects are anticipated. Furthermore, by combining them with transparent solar cells applicable to glass surfaces, they could further propel the realization of truly carbon-neutral mobility.
Nanomaterial technology aims to reduce energy consumption and create a comfortable interior environment.
Hyundai and Kia are pursuing various efforts to provide their customers with enriching and convenient mobility environments. The pressure-sensitive material and radiative cooling film developed using imperceptibly small nanotechnology are also outcomes of these efforts.

The ‘Pressure-Sensitive Material’ unveiled by Hyundai and Kia transforms applied pressure into electrical signals without the need for separate sensors. This technology is integrated in heating seat foam to accurately heat only the areas pertaining to passengers’ body types, effectively suppressing unnecessary heating in other areas, thereby helping to reduce power consumption and allowing for increased driving range in electrified vehicles.
Carbon Nanotubes (CNT) were utilized in developing this material. Carbon nanotubes are carbon structures with diameters of a few nanometers, boasting tube-like characteristics, which makes them lightweight, strong, and excellent in electrical and thermal conductivity.
When pressure exceeding a certain level is applied to the seat, the contact area increases, reducing resistance and increasing current flow, leading to localized heating in that area.
Hyundai and Kia have independently designed a process to uniformly disperse this material in a special solution and coat it onto sponge-like seat foam. The solution was coated as thinly as possible to maintain the flexible physical properties of the seat foam while ensuring durability to withstand repeated friction.
The pressure-sensitive material is expected to provide new value and convenience to customers as it can link with various future technologies. In the autonomous driving era, it is anticipated to allow precise posture detection of passengers, and potentially detect biosignals like breathing and heart rate for health diagnostics.

Radiative cooling occurs when the amount of heat emitted by an object exceeds the amount absorbed. The ‘Transparent Radiative Cooling Film’ developed by Hyundai and Kia attaches to the vehicle glass to reduce the rise in interior temperature without requiring additional energy use, presenting an eco-friendly technology.
This multi-layered film structure successfully scales up to large-area applications, allowing it to be used in vehicle glass, a world-first achievement.
This material blocks incoming heat from ultraviolet, visible, and near-infrared rays while effectively radiating heat in the far-infrared range for optimal radiative cooling.
Unlike existing tinting films that simply block external heat, the transparent radiative cooling film also allows heat to be emitted outside, improving the vehicle’s internal environment while achieving carbon reduction benefits.
According to Hyundai and Kia’s internal testing, vehicles fitted with the radiative cooling film showed an indoor temperature reduction of up to 7 degrees Celsius compared to those with standard tinting films. This significant reduction is expected to lead to a decrease in carbon emissions during vehicle operation by approximately 0.3-0.8% due to reduced air conditioning usage right after entering the car in summer.
As vehicles become more integrated with electric and other types of mobility’s broader glass areas, the relevance of this technology will likely increase. Furthermore, applying it to critical areas in buildings or solar cells during the summer season will facilitate efficient thermal management and carbon reduction without additional energy use.
Song Seung-hyun, head of the Basic Materials Research Center at Hyundai and Kia, emphasized that, “The nano-based technologies presented today are the result of continuous efforts made by our material experts at Hyundai Motor Group. Nanomaterial technology will be a pivotal key in leading changes in the mobility industry.”
On the 21st (Friday), Hyundai and Kia will invite university students majoring in materials science and related fields to share development experiences about nanomaterials during the second day of the ‘Nano Tech Day 2023’ event. They will also provide a separate job consultation booth to guide students interested in employment regarding specific R&D roles and the hiring process.

In conclusion, this impressive initiative highlights the relentless drive of Hyundai and Kia towards enhancing customer experience through innovative nanotechnology in the automotive industry.
The reason that this development is ground-breaking extends to the fact that it combines elements of comfort, efficiency, and safety to push the automotive frontier to new heights.