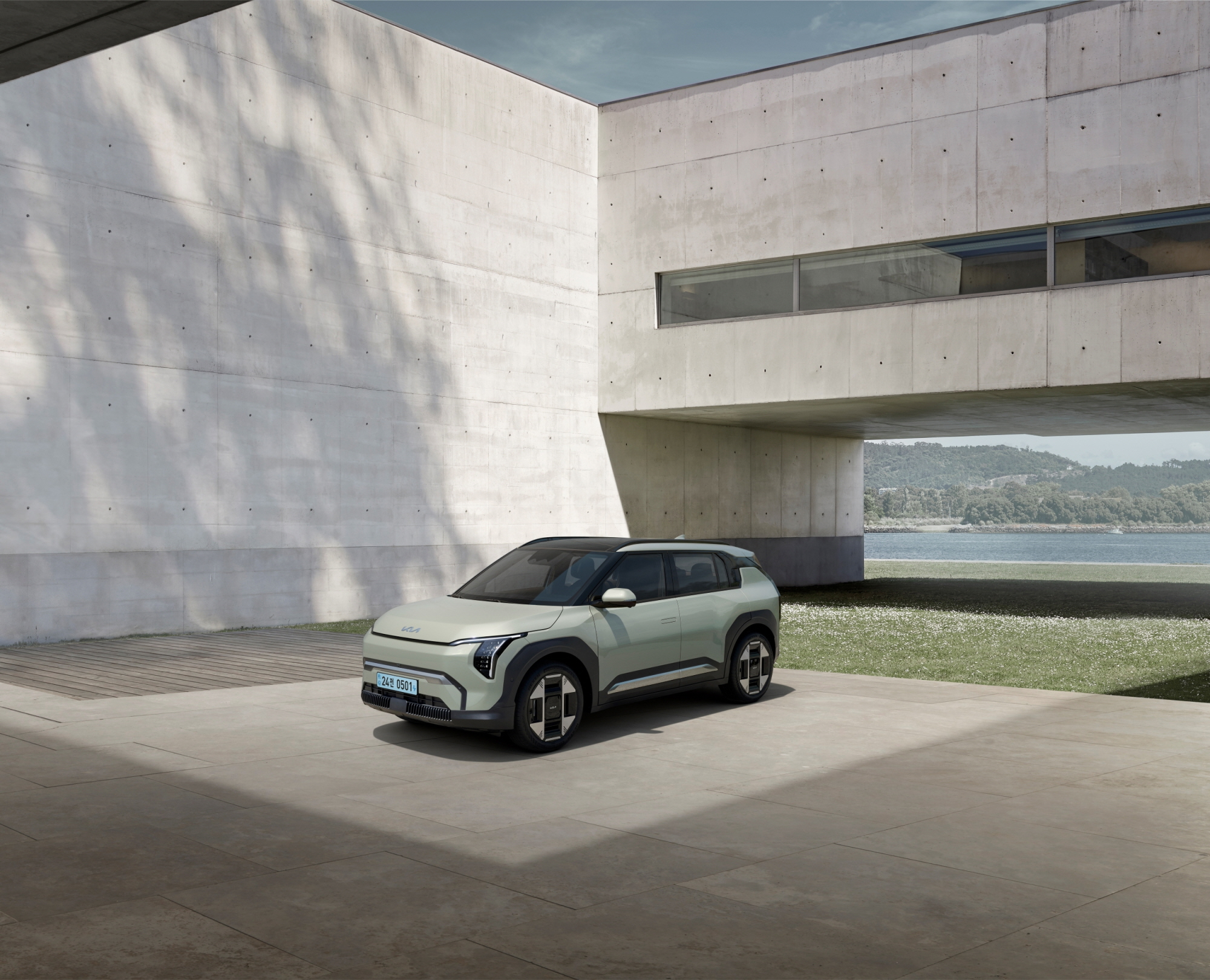
Kia has established a system that quickly informs customers of any abnormal battery conditions detected by the Battery Management System (BMS) through text messages, starting from the 21st (Wednesday).
Thanks to the application of the latest battery system monitoring technology in the BMS, possible abnormal signs can be detected rapidly. When such signs occur, the BMS will execute necessary safety controls and send messages to customers based on the severity of the risk, guiding them for inspection or emergency assistance.
Kia is implementing a comprehensive ‘Electric Vehicle Customer Care Program’, which includes the preliminary diagnosis of abnormal signs detected by the BMS, striving to ensure customer convenience for electric vehicle users. This includes: ▲Providing reassurance inspection services for electric vehicles ▲Strengthening basic battery inspections ▲Applying the latest BMS battery systems.
[Electric Vehicle Reassurance Inspection Service]
Kia has recently rolled out an electric vehicle reassurance inspection service that includes the diagnosis of high-voltage battery status. Free inspections are being conducted on a total of 9 critical items, including high-voltage battery status, cooling systems, fault diagnostics, and external damage. An emergency situation room is also operational to prepare for urgent situations.
The electric vehicle reassurance inspection service can be accessed through the nationwide A/S network, and if an issue with the battery is confirmed, customers can exchange the battery pack free of charge within the warranty period.
[Strengthening Basic Battery Inspections]
Kia plans to enhance the ‘Members Basic Inspection’ (formerly regular inspection) service related to batteries to support customers’ long-term safe operation. The Members Basic Inspection is a free inspection conducted annually for the first 1 to 8 years after vehicle purchase, where electric vehicle owners can have their high-voltage battery and other vehicle components checked, allowing them to verify their vehicle’s safety each year.
Customers can have their high-voltage battery, motor cooling fluid, and high-voltage wiring inspected, with inspection items varying by year. To strengthen the basic inspection service, Kia plans to provide diagnostic reports on battery performance status after evaluations.
Kia acknowledges that many customers are worried about battery damage from impacts due to speed bumps or uneven road surfaces, and during the Members Basic Inspection, the condition of the customer’s vehicle battery case will also be explained. Kia will thoroughly inform customers that the battery pack is designed to withstand various mechanical tests, such as impacts, drops, and compressions, to eliminate any concerns about fire hazards from general driving impacts.
[Application of Latest BMS Battery System Monitoring Technology]
Finally, Kia plans to apply the latest BMS battery system monitoring technology across all models ahead of schedule. One of the critical functions of the BMS is precise ‘battery system monitoring’, and the technology for monitoring battery systems has been continually evolving, including techniques for detecting instantaneous and minor shorts.
Kia plans to apply instantaneous and minor short detection technology to new vehicles for sale, while also developing software update tools for previously sold electric vehicles to be phased in by the end of the year.
A representative from Kia’s Domestic Business Headquarters stated, “Based on the accumulated safety technology and expertise, we will make our best effort to alleviate customers’ concerns about electric vehicle safety by providing various safety devices and customer service touchpoints.”
Jin Sang Lee daedusj@autodiary.kr