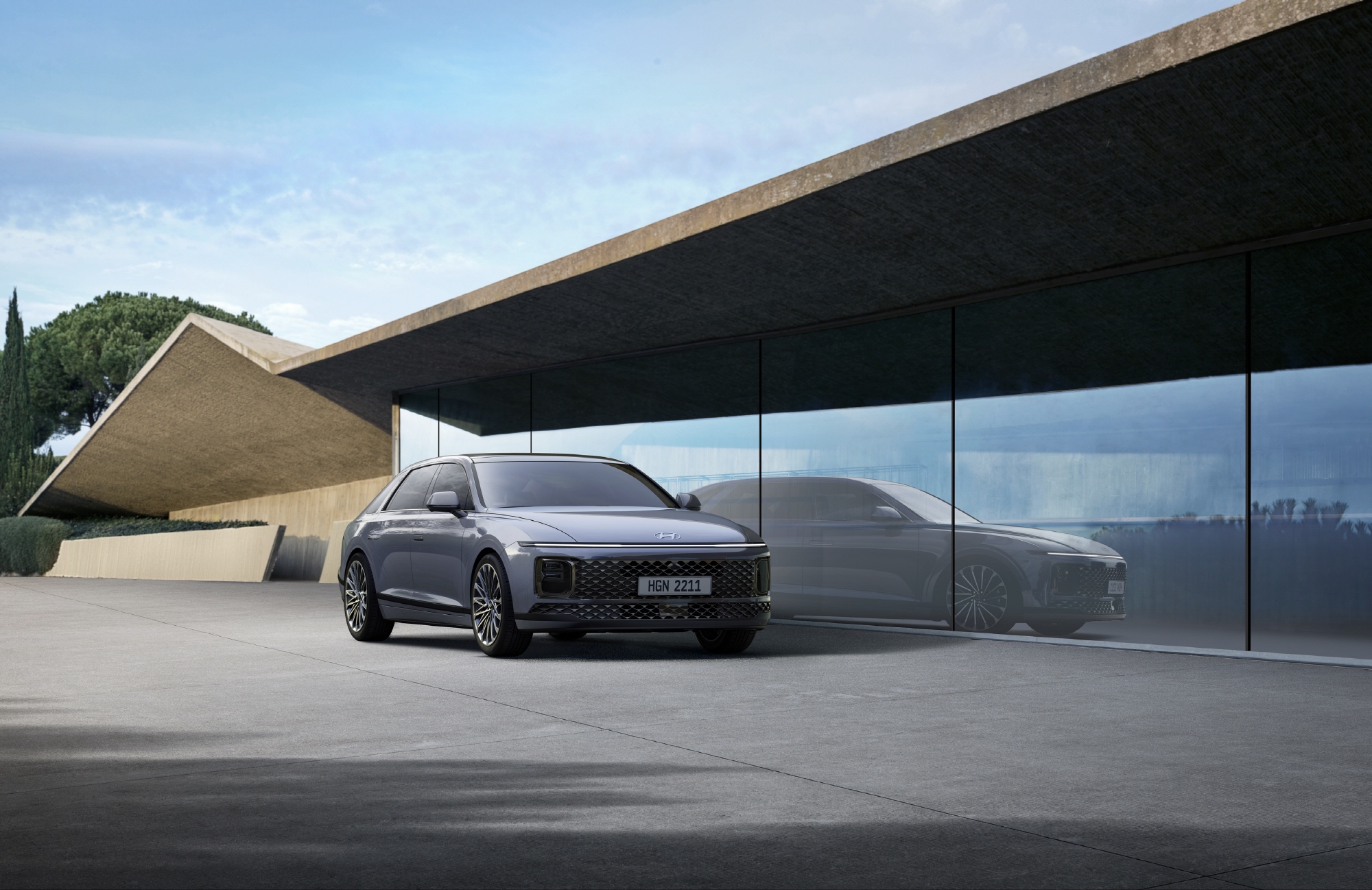
Hyundai Motor Company and its labor union have reached a provisional agreement for the 2023 labor-management negotiations.
On the 12th, during the 21st labor negotiations held at the Ulsan factory headquarters, more than 60 labor and management bargaining representatives, including CEO Lee Dong-seok and union branch president Ahn Hyun-ho, reached a provisional agreement.
The negotiations were concluded without a strike, achieving a fifth consecutive year of peaceful provisional agreements since 2019. This marks the first time in history since the establishment of the union in 1987 that there have been five consecutive years without conflict.
In light of the increased market uncertainties due to the global economic recession, the Russia-Ukraine war, high oil prices, and inflation, Hyundai and the union agreed to maintain a stable production system to lay the foundation for overcoming the crisis.
In this provisional agreement, both parties established a ‘special agreement for future shared growth’ aimed at transforming domestic plants into core manufacturing bases for long-term future business while specifying the investments related to domestic factories that were agreed upon in last year’s negotiations.
The company plans to enhance the use of aluminum bodies in vehicles to push forward with electrification and lightweighting of vehicles. To achieve this, they will actively pursue the internalization of ‘Hyper Casting’ technology, an advanced large die-casting body manufacturing method. This will involve selecting suitable sites, including idle spaces from existing engine and transmission plants, and if the necessary conditions for manufacturing competitiveness are met, mass production is targeted for 2026.
Additionally, both parties plan to construct a multifunctional, multipurpose production plant to develop and produce luxury models or limited editions that cannot be manufactured on existing production lines due to their inability to meet mass production and sales demands. They agreed to invest in this facility if the conditions regarding business feasibility and productivity are met.
Moreover, the parties agreed to establish selection and placement criteria for personnel who will work at the new electric vehicle plant scheduled for completion in 2025, and to develop and operate special training programs for these staff members.
Hyundai’s labor and management have recognized the seriousness of the low birthrate issue, a newly emerging social problem, and have formed a joint ‘Low Birthrate/Childcare Support TFT’ outside the labor negotiations to draft a ‘special agreement on low birthrate measures related to life cycles’ for employees concerning pregnancy, childbirth, and parenting. This represents a new paradigm in Hyundai’s negotiations.
To assist employees and their families with pregnancy, the company has extended paid leave for infertility from 3 days to 5 days and will support infertility treatment costs up to 1 million won per session, without limit on the number of sessions.
As part of childbirth support measures, the benefits have been significantly increased: 3 million won for the first child, 4 million won for the second, and 5 million won for the third child and beyond. A new ‘Mom and Dad Voucher’ system will provide vouchers of 500,000 won for the first child, 1 million won for the second child, and 1.5 million won for the third child and beyond.
Support measures for child-rearing have also been significantly enhanced. The educational expenses for children aged 4 to 5 will be increased to 2.4 million won over two years. Additionally, the period in which parents can reduce work hours for childcare has been extended, and vouchers of 500,000 won for the first child, 1 million won for the second, and 1.5 million won for the third child and beyond will be provided as a reward for celebrating a child’s first day of school.
Furthermore, Hyundai’s labor and management are seeking various ways to contribute to solving social issues and coexisting with local communities. They have decided to actively address the youth unemployment problem and create domestic jobs by implementing additional hiring for technical positions in production areas.
Following an agreement last year to hire 400 employees in 2023 and 300 in 2024, they have now agreed to recruit an additional 500 technical staff in 2024 and 300 in 2025.
The company intends to focus hiring on specialized personnel in electrification and manufacturing technology innovation, determining the timing and method of hiring based on various conditions such as workforce management and technological changes. Both parties agreed to increase the existing annual social contribution fund from 5 billion won to 6 billion won to enhance their social contribution activities toward marginalized and underprivileged groups.
In terms of wages and performance incentives, an agreement was reached, taking into account the challenging management environment due to global supply chain disruptions and geopolitical risks, reflecting the best operational performance achieved last year and exceeding this year’s business targets. Major points include a 4.8% increase in the base salary (111,000 won, including promotion), a performance bonus of 300% + 8 million won based on 2022’s business performance, a special encouragement bonus of 2.5 million won for being selected as the ‘World Car of the Year,’ a 100% encouragement bonus for achieving production/quality/safety business targets in the second half of 2023, and a separate agreement regarding the settlement of the 2023 collective negotiations involving 15 shares of stock and a 250,000 won traditional market gift certificate. (The annual salary increase rate is expected to be about 12% compared to the previous year.)
A Hyundai representative stated, “Despite the concerns and interests of various stakeholders, including customers and partners, regarding this year’s labor negotiations, we were able to conclude through dialogue between labor and management. We will strive together to produce the highest quality vehicles in return for our customers’ unwavering support.”
Jin Sang, daedusj@autodiary.kr