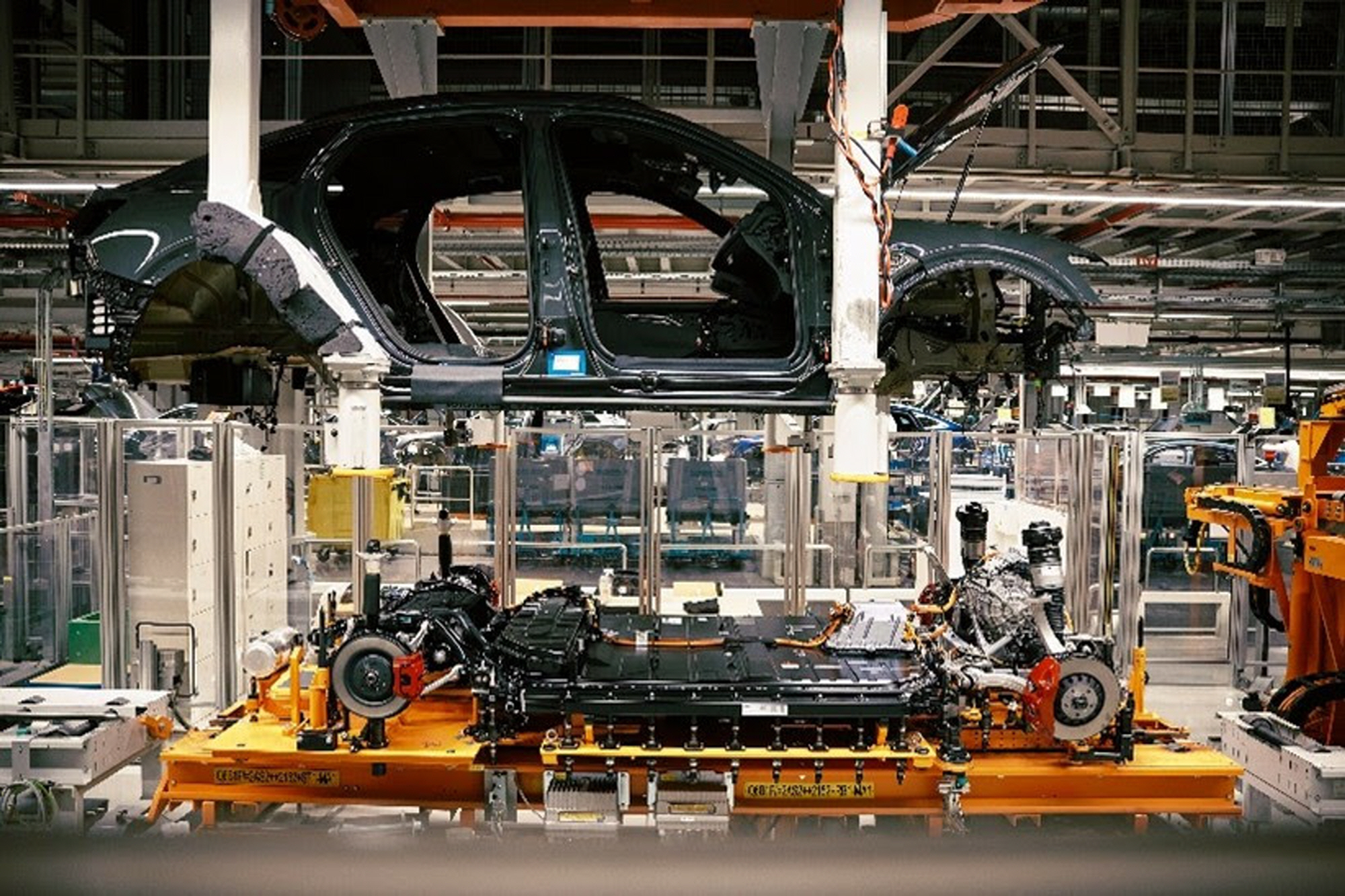
The first Q8 e-tron has rolled off the production line at Audi’s Brussels factory, marking the beginning of a new era for Audi’s top-tier electric SUV models.
Since the start of e-tron production, the Brussels factory has become a role model for sustainable manufacturing. Audi’s first electric vehicle, the e-tron, has seen approximately 160,000 units produced from 2018 to now.
Gert Walker, Director of Audi’s Production and Logistics Division, emphasized the significance of the new flagship model, stating, “The new Audi Q8 e-tron, known for its enhanced efficiency, extended range, and sleek design, sends a strong message about Audi’s commitment to electric mobility.” He also highlighted that “Brussels has played a pivotal role as a key pioneer. We have learned a great deal from our experience of exporting 160,000 vehicles worldwide,” underlining the factory’s leadership in sustainable development.
The battery assembly facility in Brussels plays a crucial role in the entire Audi Group. Unlike many competitors, Audi focuses on promoting the ‘Factory 360’ concept through internal transformation.
The Brussels factory has served as a model for specific areas of the innovative Factory 360 concept. By investing in existing facilities, Audi pursues ‘active sustainability’ economically, ecologically, and socially.
Walker emphasized, “Audi has chosen the path of conserving resources and promoting change.” Additionally, Xavier Ross, Director for Human Resources and Organization, noted that the Brussels facility offers valuable insights into specific employee training programs, stating, “The experiences gained in Brussels since 2018 can be leveraged across Audi Group factories.”
Volker Germann, CEO of Audi Brussels, also stressed the role of employees, stating, “Producing the Audi Q8 e-tron requires more than just infrastructure. Ultimately, it is the team of passionate employees that makes vehicle production possible.”
The Audi Q8 e-tron has received carbon-neutral vehicle certification, making its way to European and American consumers. From 2025 onwards, all Audi factories will engage in carbon-neutral production as part of the in-house environmental project Mission Zero.
However, the Brussels factory, which earned the title of “Factory of the Future” from the Belgian Entrepreneurial Union Agoria in 2020, began its differentiation process in 2018. With the onset of e-tron production, Brussels became the first factory in the premium vehicle sector to achieve carbon-neutral mass production certification.
The Brussels facility began transitioning to green energy in 2012. As part of this, Audi Brussels installed the largest solar system in the region on a site of 107,000 m2, generating approximately 9,000 MWh of sustainable energy annually. This is sufficient to charge 90,000 Audi Q8 e-trons and reduce carbon emissions by 1,881 tons.
Companies supplying battery cells to the factory must exclusively use renewable energy for production, and electric drive motors are transported from Hungary to Brussels by eco-friendly freight trains. Since May 2022, Audi has been utilizing rail transport over a route of about 1,300 km, which reduces annual carbon emissions by about 2,600 tons.
AUDI AG has owned the Brussels plant since 2007. After acquiring the plant, Audi Brussels transformed it into a production base for the new model line A1.
Subsequently, in 2018, the Audi e-tron was born. Audi Brussels produced a total of 43,866 pure electric vehicles in 2021. From the first half of 2023, over 3,000 employees will be engaged in the production of the Audi Q4 e-tron at the Brussels factory.
Thanks to an optimized drive concept, improved aerodynamics, and enhanced charging performance and battery capacity, the driving range of the new Audi Q8 e-tron has increased to 582 km for the SUV model and 600 km for the sportback model, based on WLTP standards.
Audi has utilized recycled materials in some parts of the new model. These materials, recovered through recycling processes, will conserve resources and facilitate the efficient and sustainable circulation of materials.
Jin Lee daedusj@autodiary.kr