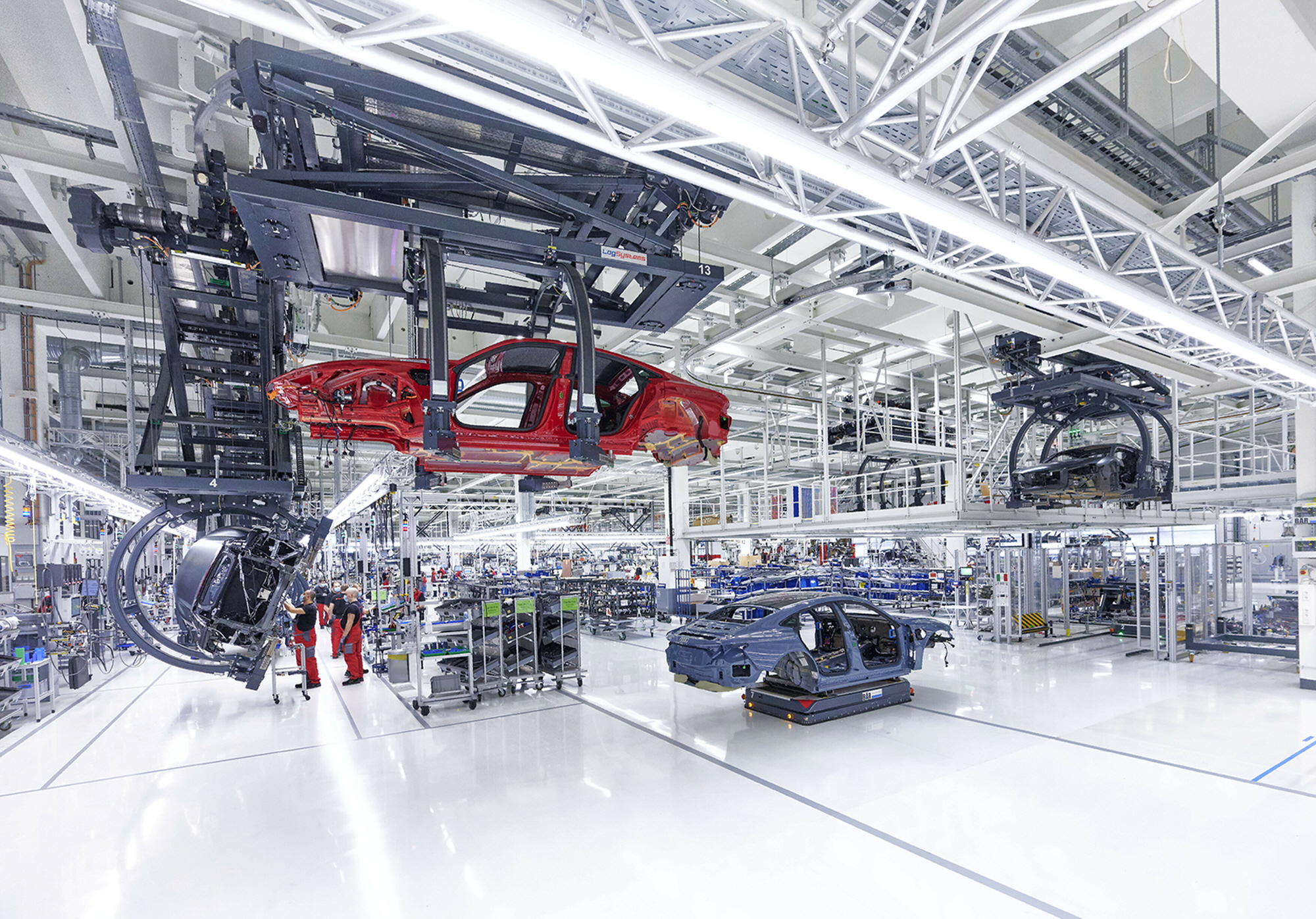
Audi has announced its ‘360 Factory’ plan and has presented its vision for electric vehicle production. By 2026, all new vehicles introduced to the global market will be pure electric models, and production of internal combustion engine vehicles will gradually cease by 2033. With a clear commitment as part of the ‘Vorsprung 2030’ strategy, Audi is now preparing to innovate its global facilities for pure electric vehicle production.
To achieve this vision, Audi is restructuring its existing global production network. Gert Walker, a member of the board overseeing production and logistics, stated, “We are systematically modernizing all our production locations.” He explained, “Instead of building new plants for electrification, we will invest in existing plants to make them as efficient and resilient as new production plants or greenfield facilities.” According to Director Walker, “This is a sustainable execution plan from an economic, ecological, and social standpoint. The process Audi is undertaking is aimed at saving resources and accelerating the transition to a sustainable premium mobility provider.”
Audi aims to establish a flexible and resilient production environment to secure its long-term competitive advantage. To achieve these goals, Audi has developed a comprehensive strategy that considers various perspectives. Director Walker and his team created Audi’s future vision of the ‘360 Factory’ based on questions such as, “What does society expect from us? What do customers demand? What are stakeholders’ expectations, and what will employees need in the future?” This approach was born out of a balanced examination of cost efficiency, sustainability, flexibility, and attractiveness.
Within the next decade, Audi will produce electric vehicle models at all its manufacturing sites worldwide.
Director Gert Walker stated, “To achieve this goal, Audi is already securing highly qualified staff and has allocated an education budget of approximately €500 million to train all employees by 2025 to prepare them for future environments.” The Bollinger Höfe and Brussels plants already produce pure electric vehicles, and starting next year, the Ingolstadt plant will begin production of the new pure electric model, ‘The New Audi Q6 e-tron.’ Additionally, production of pure electric vehicles will gradually commence at the Neckarsulm, San José Chiapa, and Zwickau plants. By 2029, every Audi plant will produce at least one pure electric vehicle model, while production of the remaining internal combustion engine models will gradually cease after ten years, depending on local conditions.
New plants will only be constructed if additional needs arise. For example, Audi, in partnership with China’s FAW, is currently building a local production plant for models based on the PPE (Premium Platform Electric) platform in Changchun, China. Slated for completion by the end of 2024, this plant will be Audi’s first facility in China to produce only pure electric vehicle models.
Electrifying the plants is merely one aspect of Audi’s vision for future production. Director Walker asserted, “We will greatly enhance productivity and optimization by modifying the processes necessary for the transition to e-mobility.” Once preparations for the future are complete, Audi’s production network will be economic, sustainable, attractive, and flexible.
Audi plans to reduce annual production costs by half by 2033 for the economic viability of vehicle production. To achieve this, Audi intends to reduce vehicle complexity, and vehicle development will follow streamlined production processes. Audi will also continue to digitize production through solutions such as ‘Edge Cloud 4 Production’ that uses local servers.
This could replace expensive industrial PCs, thereby reducing efforts like software rollouts and operating system changes. Moving forward, Audi plans to further simplify operations with another new independent modular assembly solution called ‘Cycle,’ which enables innovation and flexible collaboration in various locations while saving on materials and resources.
To respond more flexibly to changing customer demands and production programs, Audi is making its production processes more adaptable. Director Walker stated, “Audi aims to organize both products and production to provide optimum benefits to customers.” Accordingly, ‘The New Audi Q6 e-tron’ will initially be produced at the Ingolstadt plant on production lines shared with models like the A4 and A5, with electric models gradually replacing internal combustion engine models.
Since 2019, Audi has been implementing the ‘Mission Zero’ program to reduce its ecological footprint related to production and logistics. The core objective of this program is to achieve carbon neutrality at all Audi production sites worldwide by 2025. To this end, carbon neutrality has already been achieved at the Brussels and Zwickau plants, and the Bollinger Höfe plant in Neckarsulm.
Environmental programs also encompass biodiversity protection and conservation, as well as resource and water efficiency. For instance, Audi plans to halve water consumption at its production sites by 2035. In 2018, the Audi plant in Mexico became the world’s first premium car production facility with zero wastewater. Moreover, the Neckarsulm plant is starting a pilot project with a nearby municipal wastewater treatment plant, which is expected to reduce freshwater demand by over 70%.
While pursuing change with the ‘360 Factory,’ Audi has set even more ambitious sustainability goals related to production. Audi aims to halve its absolute environmental impacts by 2030 compared to 2018 figures for primary energy consumption, power plant emissions, CO2 equivalents, air pollutants, local water risks, wastewater, and waste quantities.
To achieve this goal, the focus is on producing more circular value chains that utilize resources efficiently, employing innovative technologies to generate renewable energy in-house during specified cycles.
The Audi ‘360 Factory’ will make it a workplace where everyone wants to work, both externally and internally. As part of this commitment, Audi is currently working to implement flexible working arrangements not only for general jobs but also for specific shifts and work departments, making the working environment and break rooms more comfortable for employees.
Audi’s production department sees itself not just as a vehicle manufacturer but as a process technology developer. Director Walker stated, “Audi wants to be the best employer for current employees as well as all applicants, students, and professionals,” and added, “The transition to the ‘360 Factory’ requires top talent in fields that are generally not associated with vehicle production, such as electronics and software development.”
He emphasized that the Ingolstadt plant, Audi’s first fully comprehensive ‘360 Factory,’ will serve as a blueprint for innovating large-scale production facilities across Audi’s global network. He assured that other production locations would begin transitioning gradually, noting that while many steps remain, they have already taken the first steps toward achieving their goals and executing plans correctly.
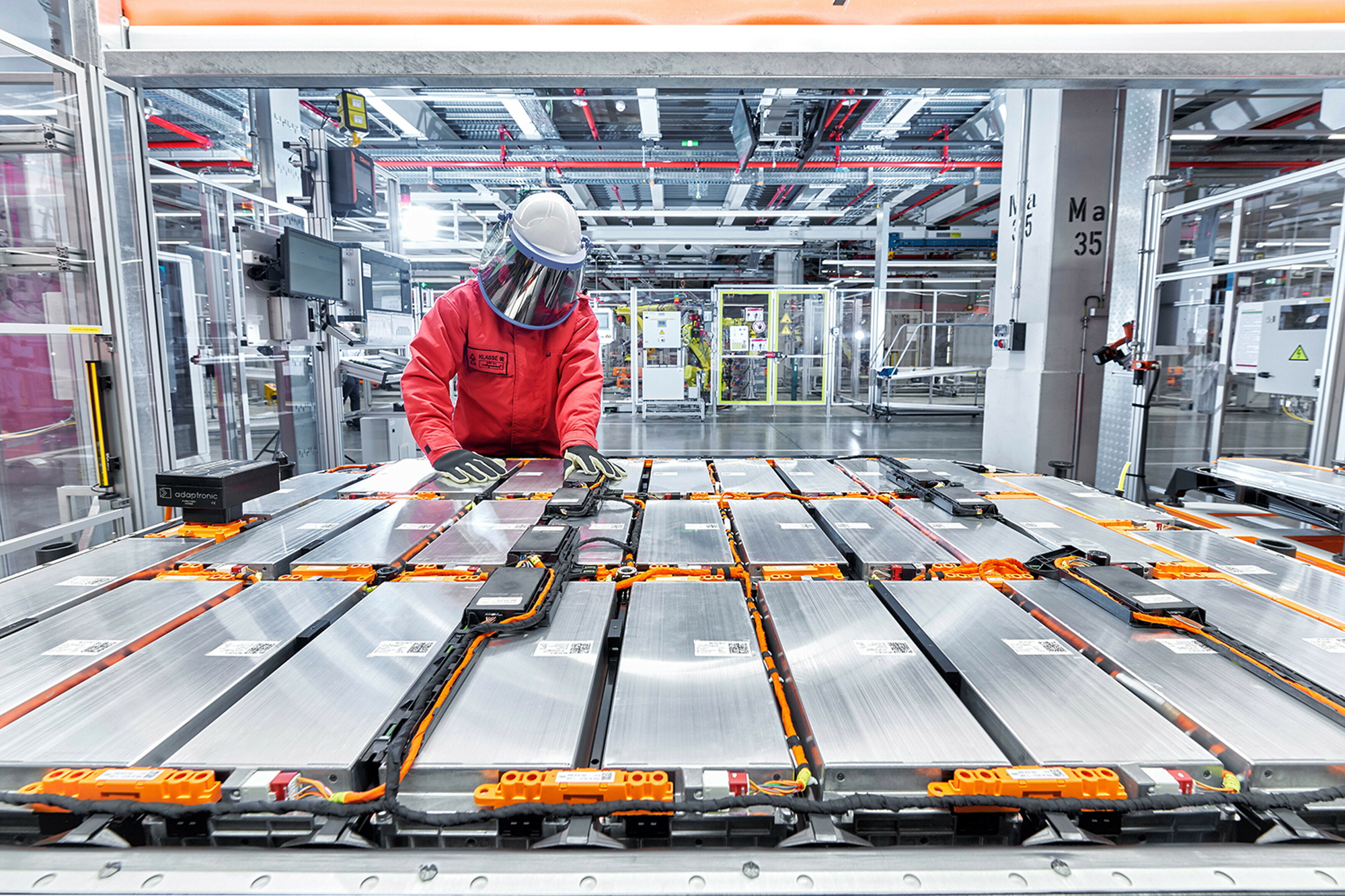
Lee Sang-jin daedusj@autodiary.kr