토요타 모토마치 공장은 멀티 패스웨이 현장
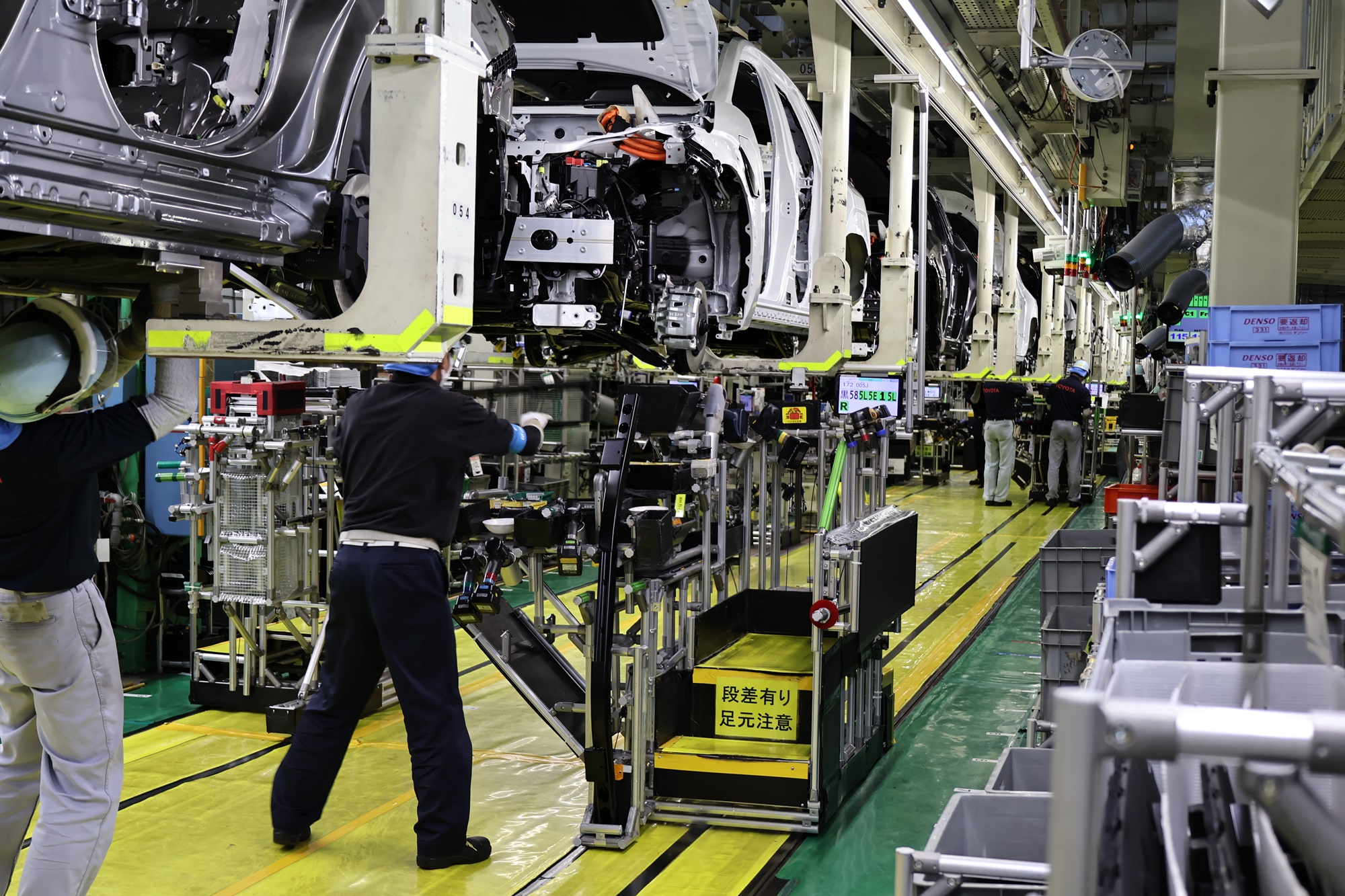
토요타 모토마치 공장은 ‘멀티 패스웨이’의 현장이었다.
토요타의 모토마치 공장은 1959년 8월부터 가동을 시작했다. 연산능력 16만 3,000대로 1만 명이 근무하고 있다. 5개 조립라인과 1개 양산 라인을 갖고있으며 양산라인에서는 9개 차종을 혼류 생산한다. 수소연료전지 차인 미라이, 크라운, 전기차인 렉서스 RZ 등이 이곳에서 양산 컨베이어를 타고 만들어진다. 렉서스 LC, 토요타 센트리 등도 별도 조립라인에서 숙련도 높은 장인들이 만들어낸다. 토요타가 강조하는 멀티 패스웨이를 눈으로 볼 수 있는 현장이다. 미야베 요시히사 공장장의 말을 빌리면 “모토마치 공장은 멀티 패스웨이 그 자체”다.
‘멀티 패스웨이’는 다양한 파워트레인을 준비해 소비자들에게 넓은 선택지를 제공한다는 의미다. 한 곳에 집중하지 않고 다양한 파워트레인을 준비한다는 토요타의 핵심 전략을 담은 말이다.
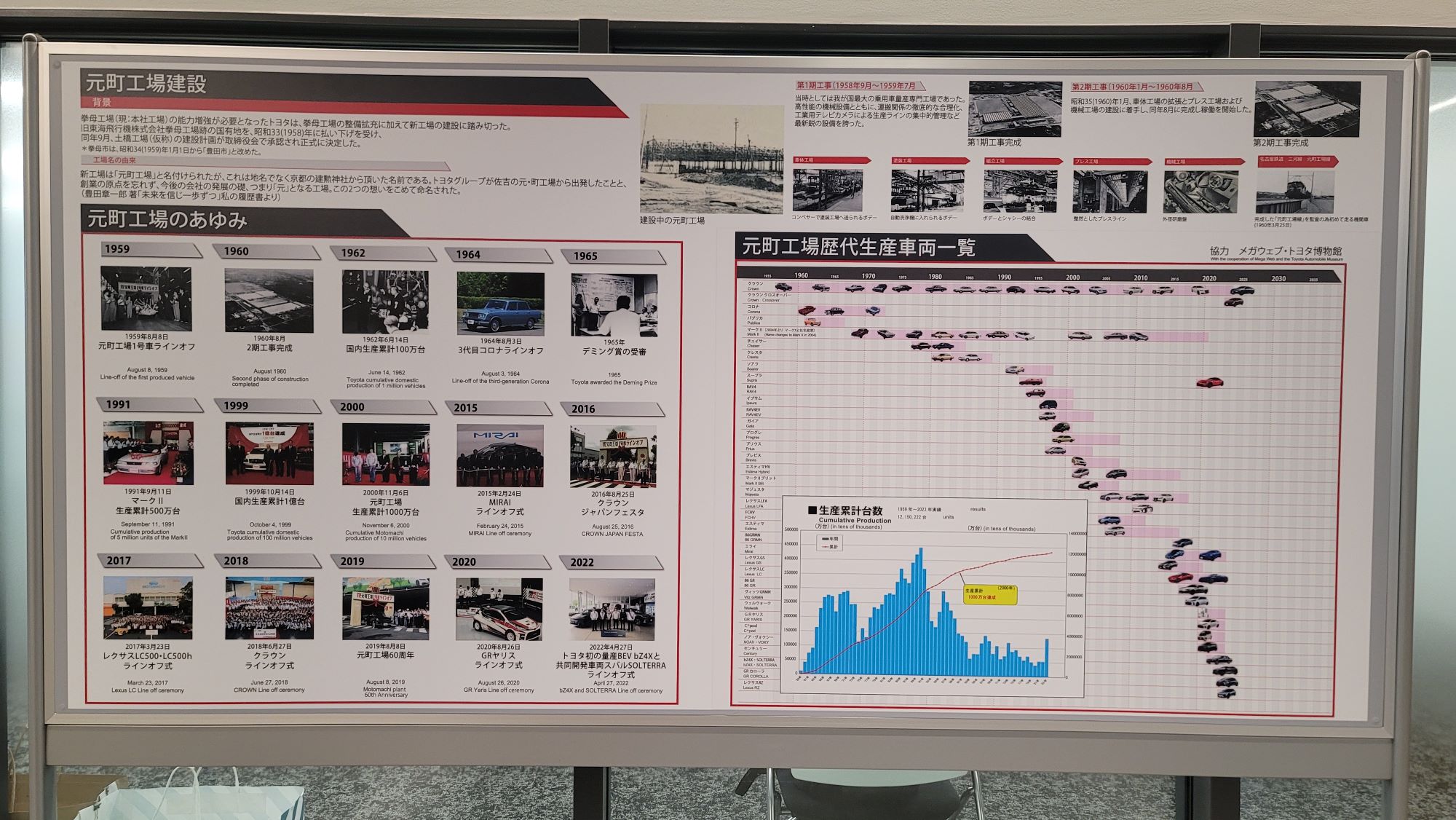
공장에 들어선 시간은 오전 9시 23분. 사인보드에는 계획대수 222대, 현재 78대 등의 숫자들이 공장 가동현황을 알려주고 있었다. 입구 근처 작업 공간에서는 여성 2인, 남성 1인이 작업을 하고 있었다. 모토마치 공장 근로자 중 여성 인력 비중은 5% 가량.
길이 1.5km의 생산 라인에는 배터리 전기차, 수소 연료전지차, 하이브리드, 내연기관 등이 앞서거니 뒷서거니 흐르고 있었다. 어떤 파워트레인이든 생산할 수 있는 건, 근로자들의 작업 편의성을 최대한 끌어올려 가능한 일이다. 테블릿에 담긴 작업지시서를 보며 근로자들은 작업한다.
근로자중 50%는 외주 인력이다. 현장 근로자들이 고민이나 선택할 일은 거의 없다. 작업 지시서를 보면 그대로 진행하면 된다. 작업지시서에는 작업할 내용, 품질 포인트 등이 포함된다. 작업 순서에 따라 정리된 부품들이 차례차례 제공된다. 근로자가 선택할 일이 없다. 부품 적기공급, 즉 저스트 인 타임(JIT)이 연출하는 현장 풍경이다.
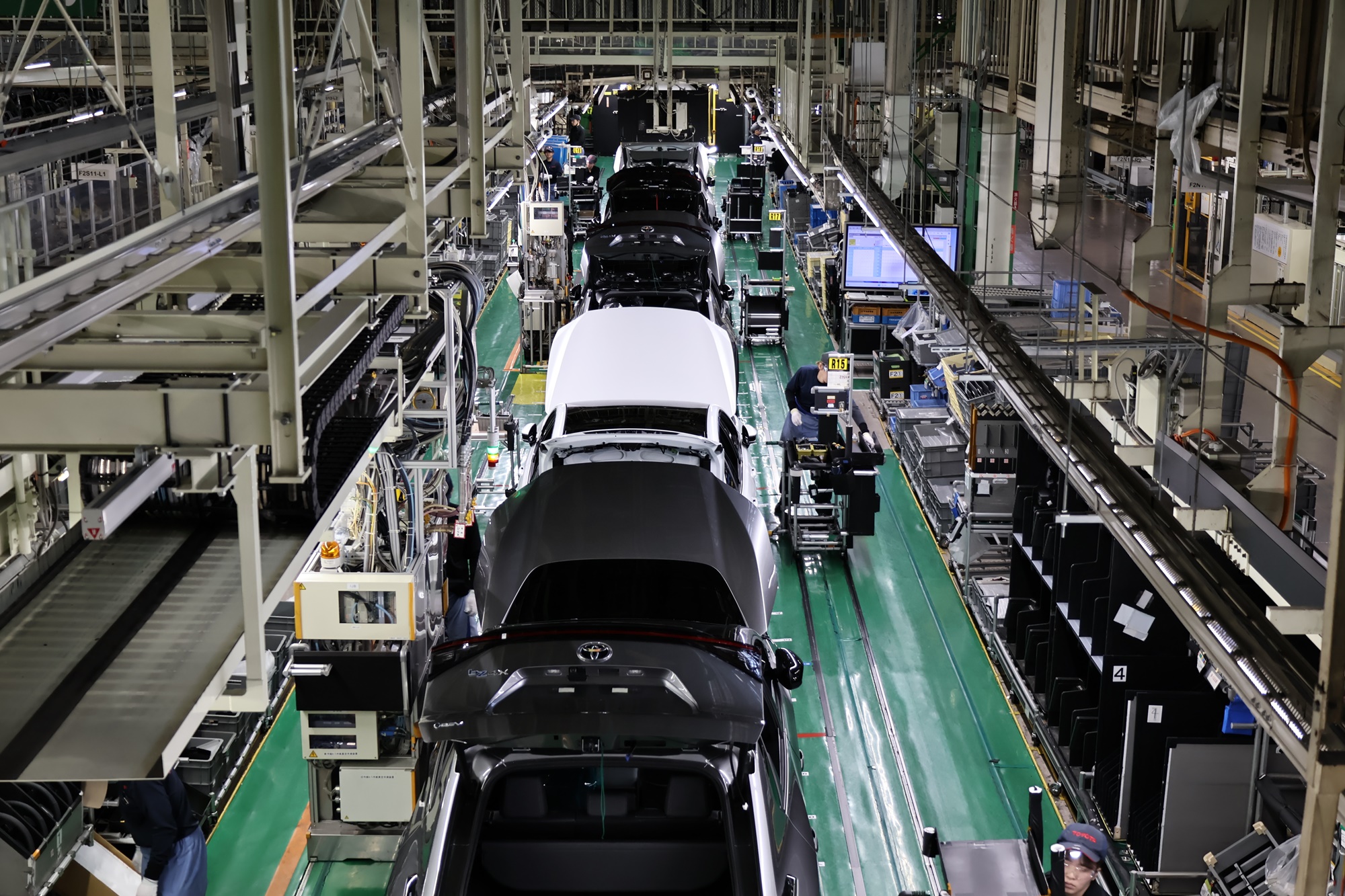
모토마치 공장은 인력과 작업량을 줄이기 위해 차량 물류 로봇(VLR : vehicle logistics robot)을 도입했다. 이 로봇은 차량의 전고/축거에 따라 화물칸을 올리거나 내리고 공간을 확장 및 수축할 수 있어 다양한 크기의 차량을 수용할 수 있다. 고정밀 자율 동작 외에도 제어 시스템이 중앙에서 여러 로봇의 동작을 관리하며 안전여부를 모니터링하고 최적의 경로를 따라 운송하도록 지원한다. 그리고 사람이 직접 진행하는 운송과는 달리 문을 열고 닫을 필요가 없어 차량을 효율적으로 배열할 수 있으며, 야적장을 보다 효율적으로 이용하는 게 가능하다.
현장에는 6m 간격으로 두 개의 버튼이 있다. 문제가 생겼을 때 이 버튼을 눌려 문제를 해결하거나 혹은 라인을 멈추게 된다. 노란색 버튼은 리더를 호출는 버튼이다. 리더를 불러 문제를 해결하면 라인은 멈추지 않고 계속 흐른다. 적색 버튼은 라인을 멈추는 버튼이지만 이 버튼을 누른다고 당장 라인이 멈추는 건 아니다. 다른 파트에서 작업 리듬을 잃지 않도록 약간의 지체 시간이 주어진다.
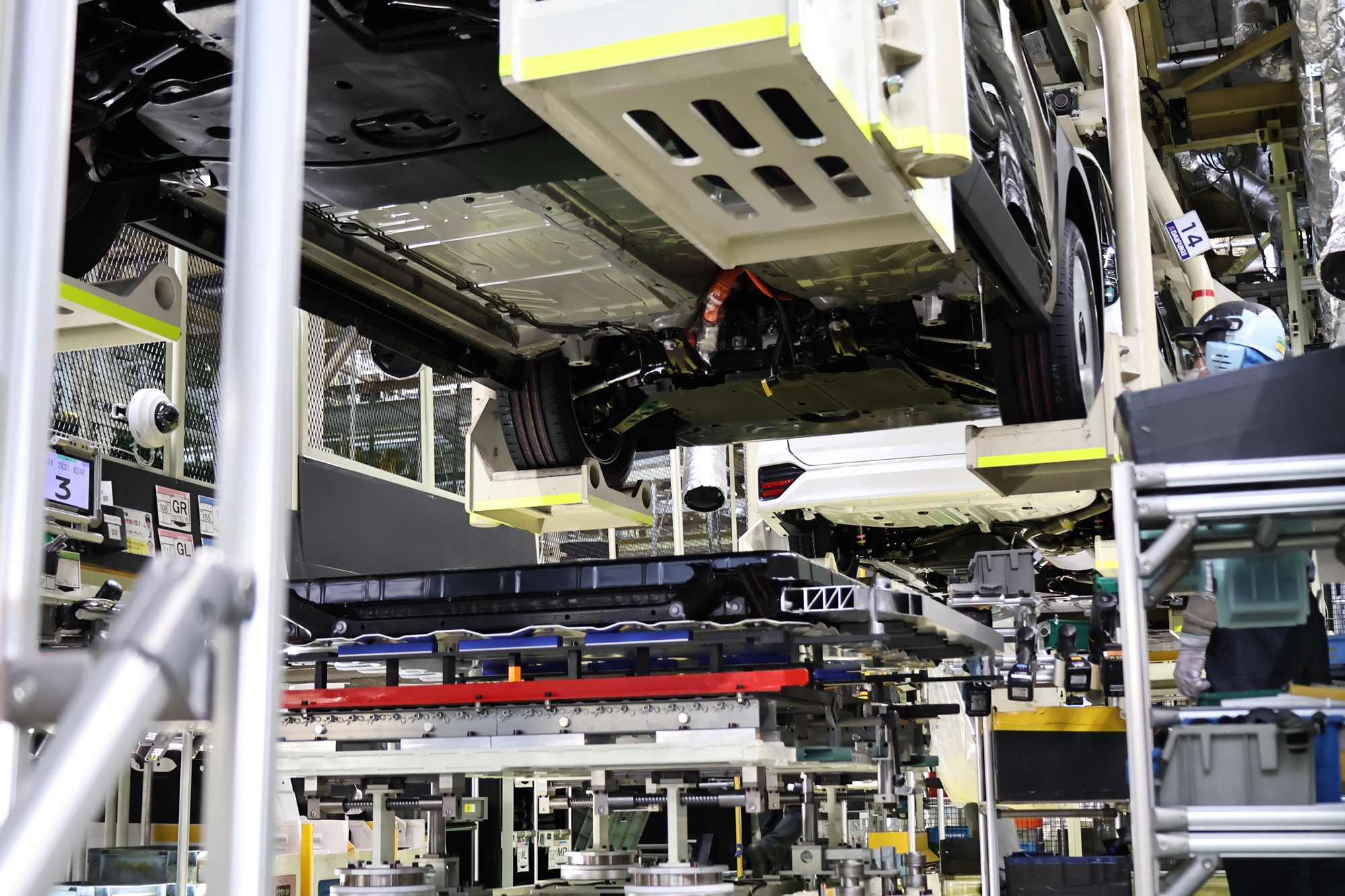
모토마치 공장은 탄소중립을 위해서도 많은 노력을 기울이고 있다. 공장에서 사용하는 지게차는 대부분 수소를 연료로 사용한다. 그 수소는 공장 인근 오니(폐기물) 처리 과정에서 발생하는 메탄을 공장까지 파이프를 연결해 가져온 뒤 99.99% 수소로 정재해 사용한다. 태양열 전기도 주요 에너지원이다. 실험실 뿐 아니라 양산 공장에서도 재생 에너지를 사용하고 있다고. 일부 섹터에서 부품 공급 라인에 중력을 이용해 무동력으로 부품을 공급하는 방법은 현장의 개선 활동을 통해 개발된 방법이라고.
렉서스 LC는 양산 라인이 아닌 조립 라인에서 숙련된 근로자인 ‘타쿠미’의 손으로 만들어진다. 작업자 1명이 차량 1대를 전담 생산하는 방식. 멈춘 듯 아주 천천히 흐르는 라인을 타고 작업이 이뤄지고 있었다. 조립을 마쳐 완성차의 모습을 갖춘 렉서스 LC는 “제품이 아닌 작품”이라고 미야베 요시히사 공장장은 강조했다. 조립 라인의 속도는 판매량이 결정한다. 2017년에 렉서스 LC를 만들기 시작할 때는 하루 48대를 만들었다. 지금은 하루 9대를 생산한다고.
일본 토요타 = 오종훈 yes@autodiary.kr
latest video
news via inbox
Nulla turp dis cursus. Integer liberos euismod pretium faucibua