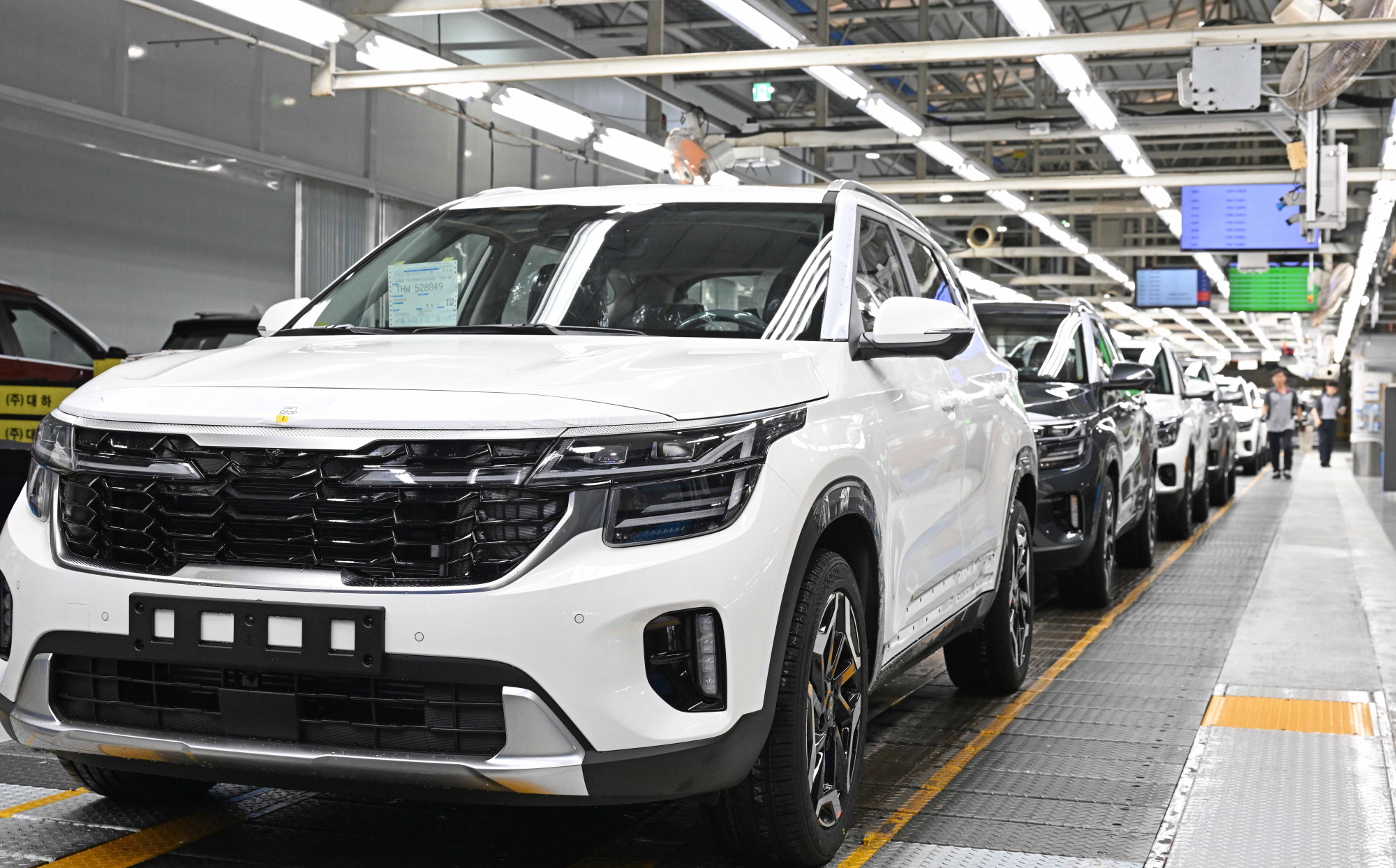
A robot dancing non-stop. In the meantime, steel plates undergo mold work, becoming the skeletal structure of a car. After going through assembly, the skeleton takes on a proper form as a car. On the 29th, I visited the production line for Kia’s bestselling model, the Celtos, at Gwangju Kia Autoland.
Gwangju Kia Autoland started in 1965 under the name Asia Motors and became part of the Hyundai Motor Group in 1998 under the Kia Motors name. It has a 36 million square meter site with an annual production capacity of 480,000 units. Gwangju Kia Autoland comprises the first factory producing the Celtos and Soul Booster, the second factory producing the Sportage and Soul, and the third factory specializing in Bonggo 3 and Bonggo 3EV. I visited the first factory that produces the Celtos and Soul Booster. The Soul has been discontinued for domestic sales and is currently only exported overseas.
The Celtos, alongside the Carnival, Sorento, and Sportage, is a crucial part of Kia’s sales strategy and is considered a prized asset in the Kia SUV lineup. As of May this year, the cumulative sales of the Celtos have reached 21,720 units, a 24.1% increase from last year’s 17,499 units, making it the fourth best-selling Kia vehicle following the Carnival, Sorento, and Sportage.
The factory entrance is bustling with forklifts transporting various materials. At the entrance, panels completed through pressing work and the panels before they are worked on are neatly stacked on pallets. The production process consists of four stages: the mold work of pressing, the body welding process, the painting process, and finally the assembly process.
Following the employee’s guidance, we moved to the pressing workshop. In the pressing workshop, robots are continuously working, buzzing as they carry out the pressing work. The pressing work happens nine times per minute, equating to 540 times an hour. The robots work joyfully, almost like they are dancing to a rhythm. The trimmings left from the pressing process slide down like on a slide, flowing to the collection point for scraps.
The panels that have undergone pressing are moved by robots for welding. The welding is done using an environmentally friendly method known as the carbon dioxide method, ensuring it’s safe for workers’ health. The completed car body then enters the painting section, where it is adorned with the various colors ordered by customers.
The color-completed car body is meticulously inspected by robots for any defects that may have occurred during the process. This is the Body Instruction (B.I) phase. While robots handled the pressing, body, and painting processes, it is now the laborers’ turn to take charge in assembly.
However, even on the assembly line, the robots continue to play a crucial role. Heavy materials that the workers cannot lift are handled by the robots.
In the assembly line where the Celtos are queued, Soul models with right-hand drive specifications occasionally appear. An employee emphasized, “The Soul and Celtos are primarily exported to Europe,” adding, “The popularity of the Soul Booster and Celtos is high within Europe.”
The employees assemble parts sequentially onto the skeletal frame dressed in colorful attire—the Celtos and Soul—adding seats, dashboards, and engines. Workers wear tense faces, focused on their assembly tasks to avoid mistakes. Their expressions convey a firm resolve not to disappoint the customers waiting for their vehicles.
Once assembled, the Celtos and Soul go through a meticulous inspection by robots, ensuring there is no error, before they are dispatched to where the customers are eagerly waiting.
Having witnessed the production process of the Celtos, my trust in Kia has increased significantly.
Lee Sang-jin daedusj@autodiary.kr